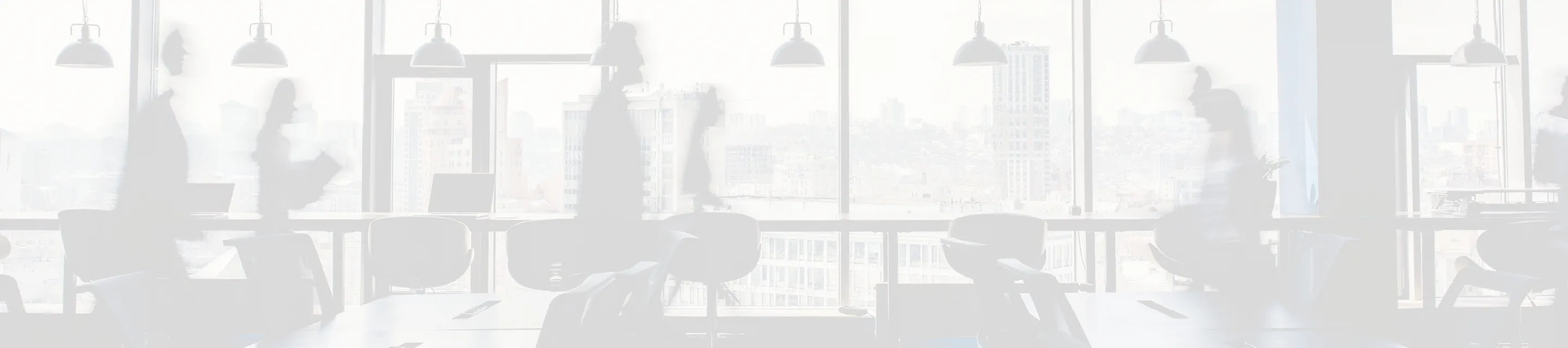
Insights
Most Recent
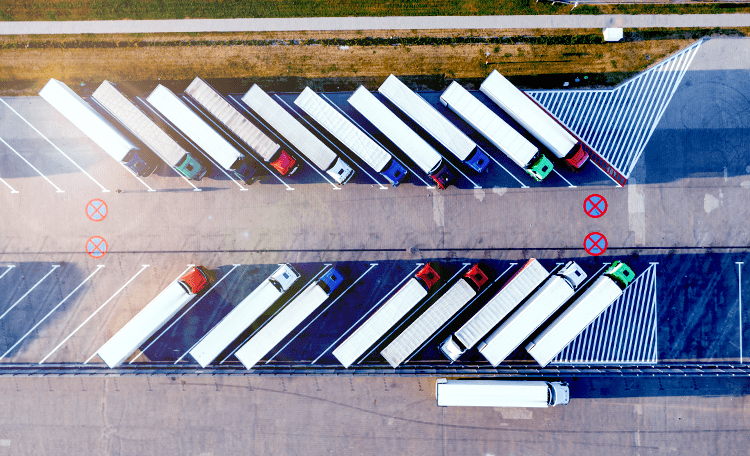
MarketBeat
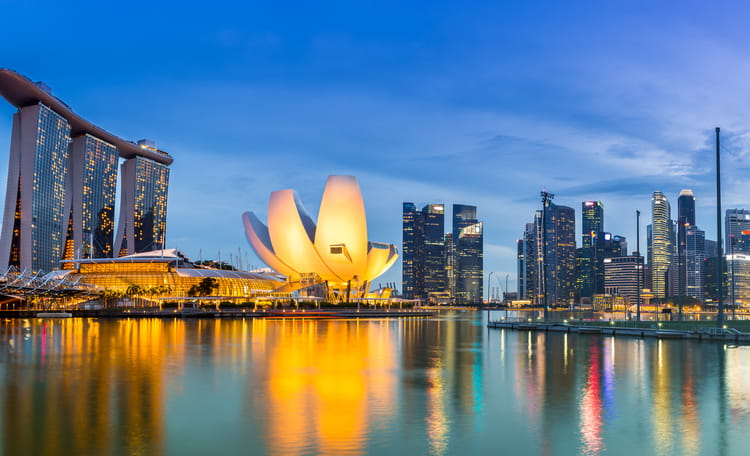
MarketBeat
Insights • Sustainability / ESG
22/05/2025
Insights • Investment / Capital Markets
Shaun Poh • 16/05/2025
MarketBeats
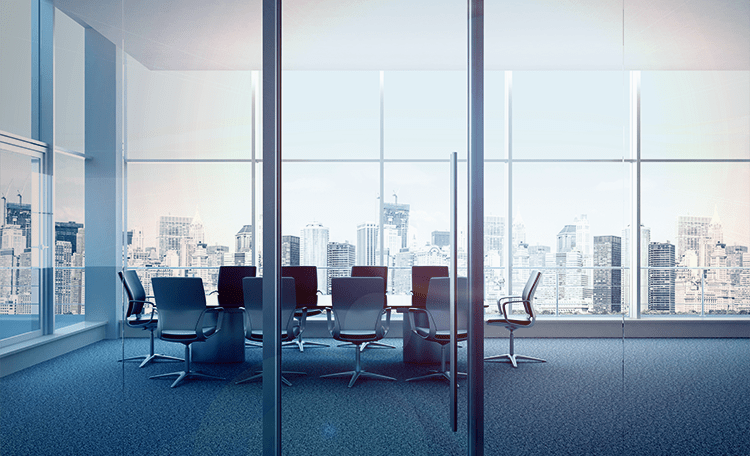
MarketBeat
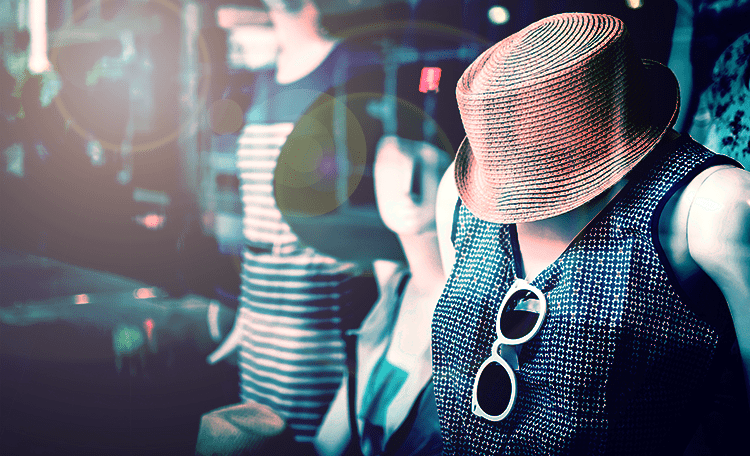
MarketBeat
Economy
Research • Labor / Talent
Aligning HR and CRE for a People-First Workplace—With Prudential Singapore
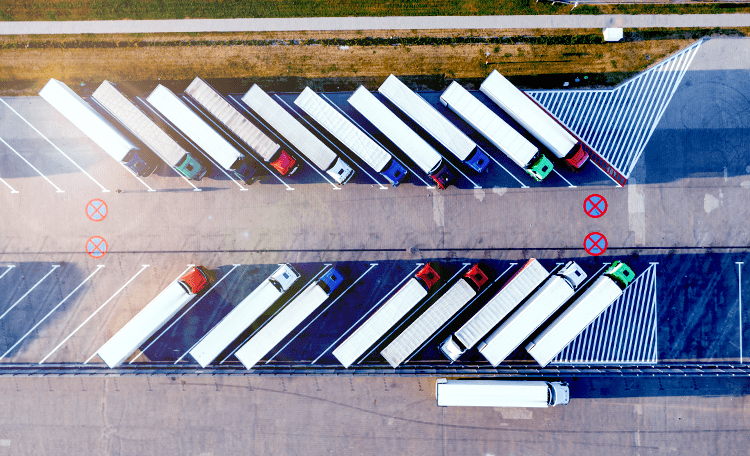
MarketBeat
Article • Economy
James Bohnaker • 26/06/2025
Logistics & Industrial
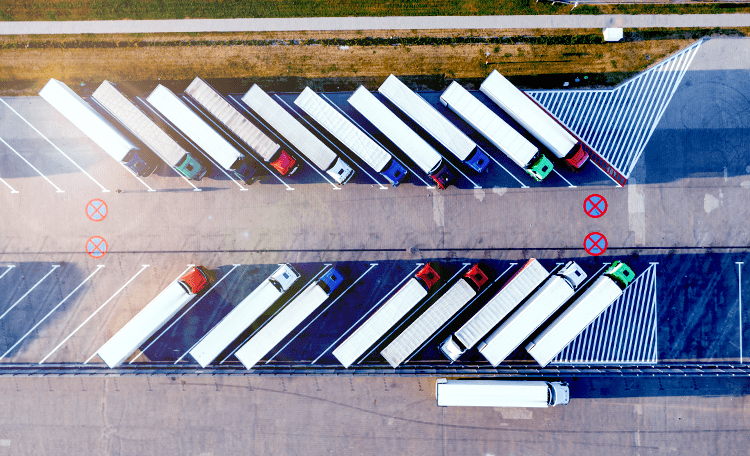
MarketBeat
Research • Sustainability / ESG
Industrial Logistics Climate Risk Outlook
Data Centres
Research
Global Data Center Market Comparison
Research
Insights • Technology
James Normandale • 16/01/2025
Insights • Technology
James Normandale • 16/01/2025
Office
Research • Labor / Talent
Aligning HR and CRE for a People-First Workplace—With Prudential Singapore
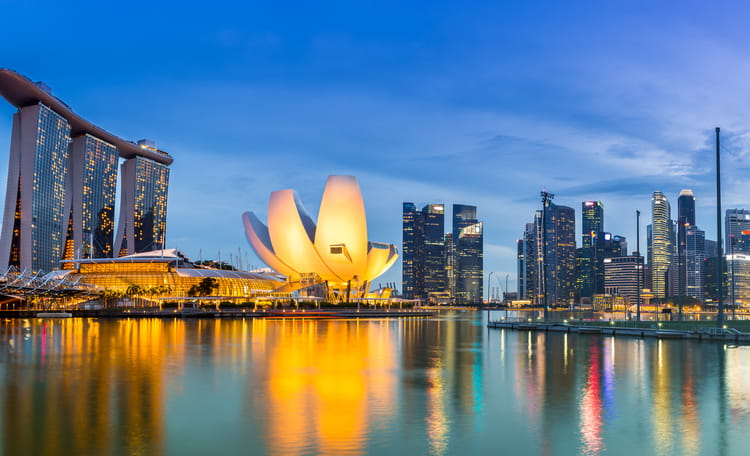
MarketBeat
Retail
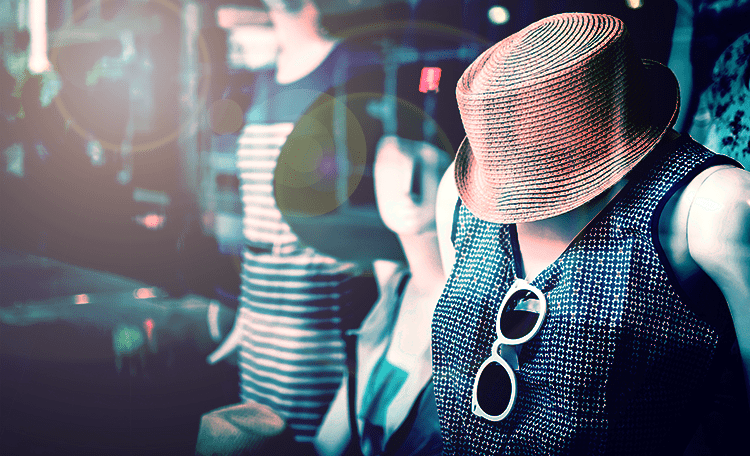
MarketBeat
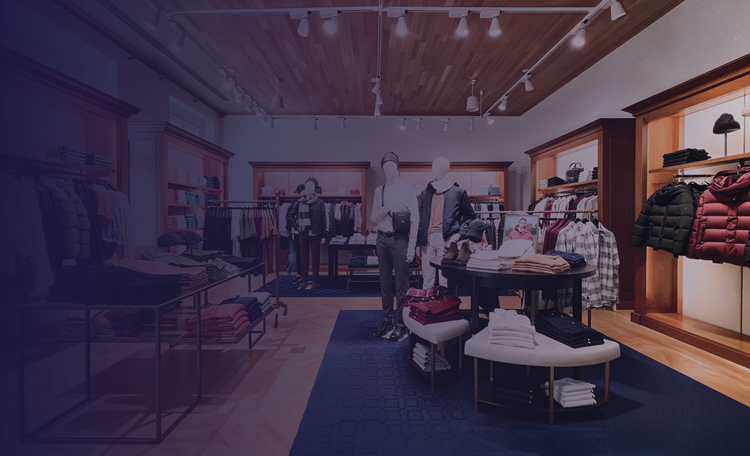
Research
Research • Food & Beverage
Jennifer Milne • 02/07/2024
Podcast • Workplace
Michael Creamer • 16/11/2022
Workplace
Insights • Workplace
Podcast • Workplace
Phillip Kelloff • 09/07/2024
Sustainability
Research • Sustainability / ESG
Industrial Logistics Climate Risk Outlook
Insights • Sustainability / ESG
Boost Your Building's Energy Efficiency: Stay Ahead of Singapore's New MEI Regime
Insights • Sustainability / ESG
Xian Yang Wong • 22/10/2024
STAY TUNED FOR THE LATEST MARKET INSIGHTS AND UPDATES
FEATURED MARKET REPORTS
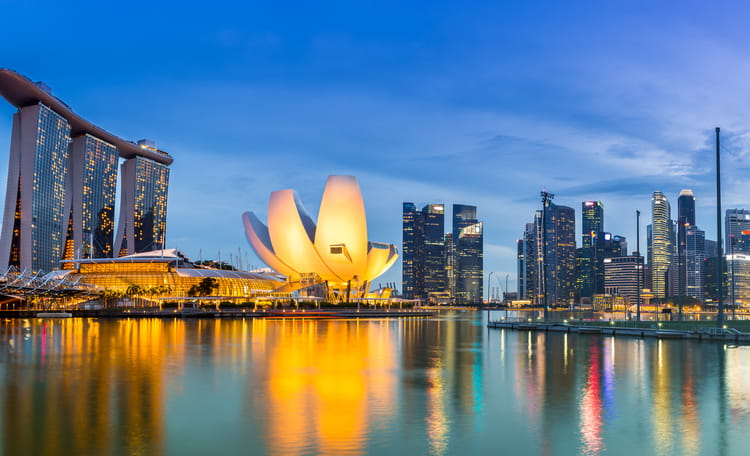
MarketBeat
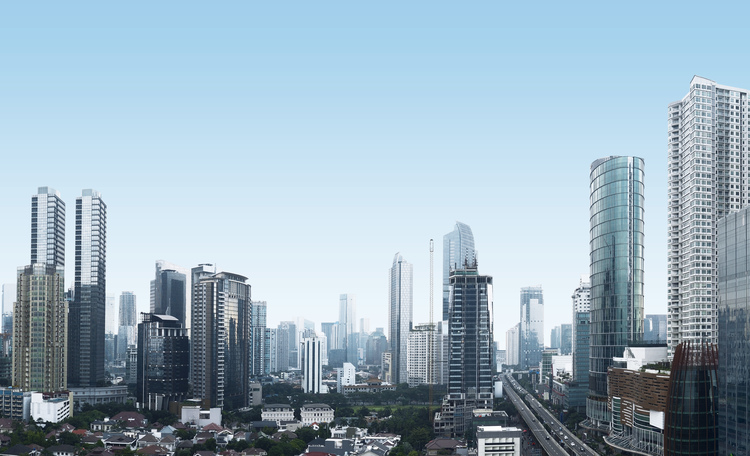
MarketBeat
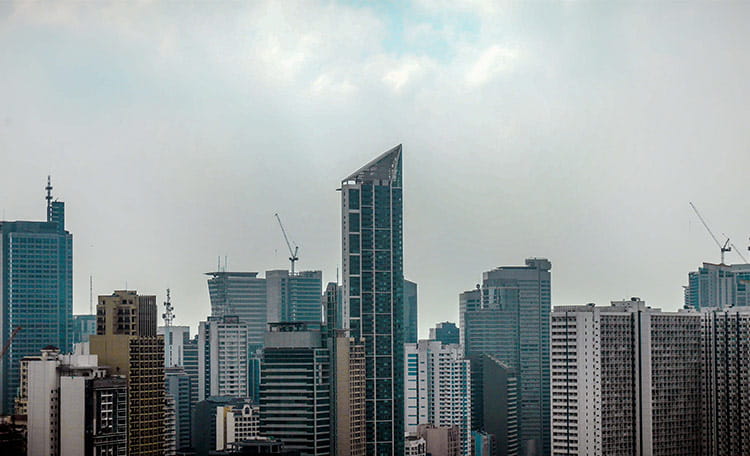