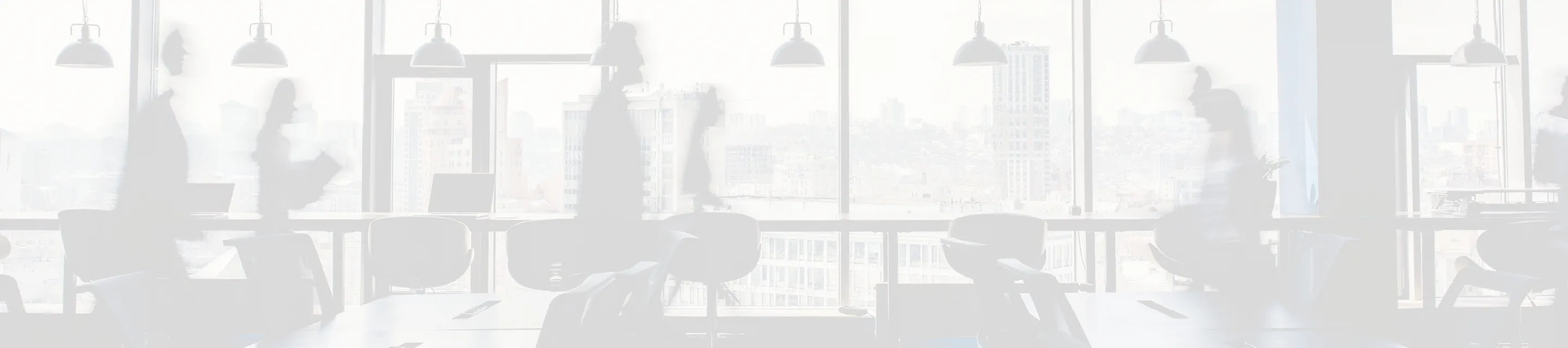
Insights
Most Recent
Insights • Sustainability / ESG
Boost Your Building's Energy Efficiency: Stay Ahead of Singapore's New MEI Regime
Insights • Investment / Capital Markets
Shaun Poh: Growing Demand for Singapore Hospitality Assets
Insights • Investment / Capital Markets
28/04/2025
Research • Economy
Xian Yang Wong • 24/04/2025
MarketBeats
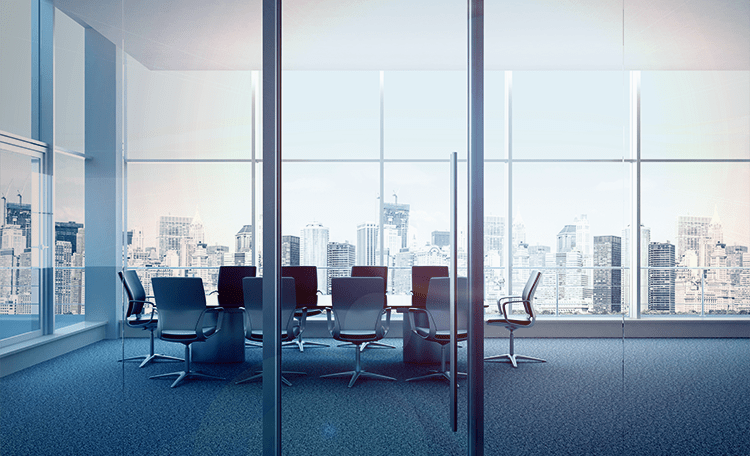
MarketBeat
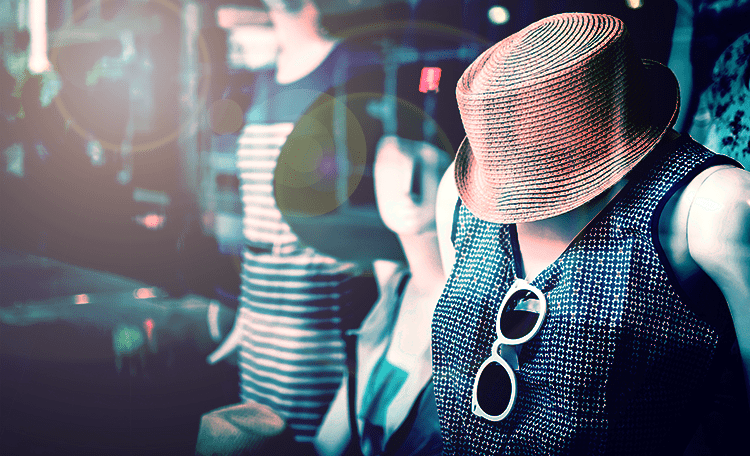
MarketBeat
Economy
Article • Economy
The Iran Situation: Implications for the Global Economy and Property Markets as of June 26, 2025
Research • Investment / Capital Markets
Abby Corbett • 05/06/2025
Logistics & Industrial
Research • Sustainability / ESG
Industrial Logistics Climate Risk Outlook
Research
Waypoint: Global Industrial Dynamics 2025
Data Centres
Research
Global Data Center Market Comparison
Research
Insights • Technology
James Normandale • 16/01/2025
Insights • Technology
James Normandale • 16/01/2025
Office
Research
What Occupiers Want: Global Survey Results 2025
Retail
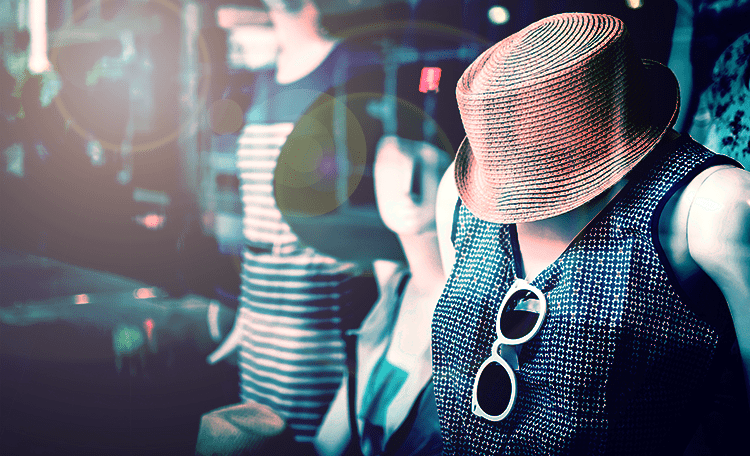
MarketBeat
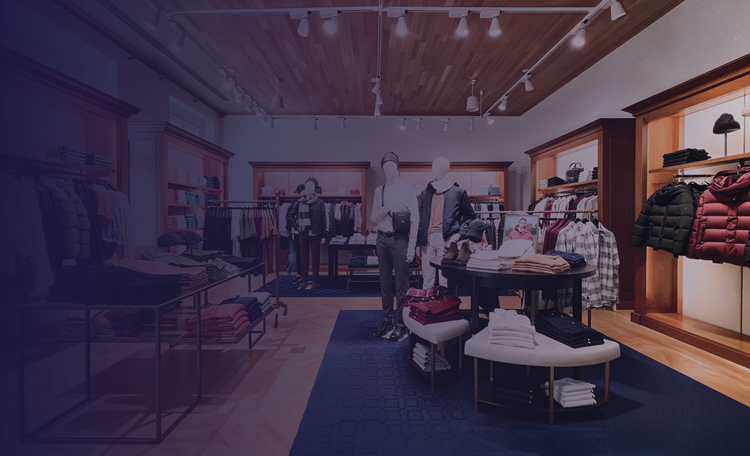
Research
Research • Food & Beverage
Jennifer Milne • 02/07/2024
Podcast • Workplace
Michael Creamer • 16/11/2022
Workplace
Insights • Workplace
Podcast • Workplace
Phillip Kelloff • 09/07/2024
Sustainability
Research • Sustainability / ESG
Industrial Logistics Climate Risk Outlook
Insights • Sustainability / ESG
Boost Your Building's Energy Efficiency: Stay Ahead of Singapore's New MEI Regime
Insights • Sustainability / ESG
Xian Yang Wong • 22/10/2024
STAY TUNED FOR THE LATEST MARKET INSIGHTS AND UPDATES
FEATURED MARKET REPORTS
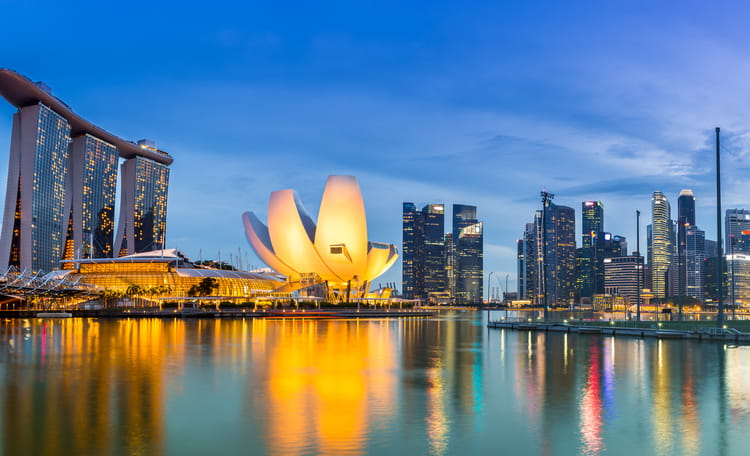
MarketBeat
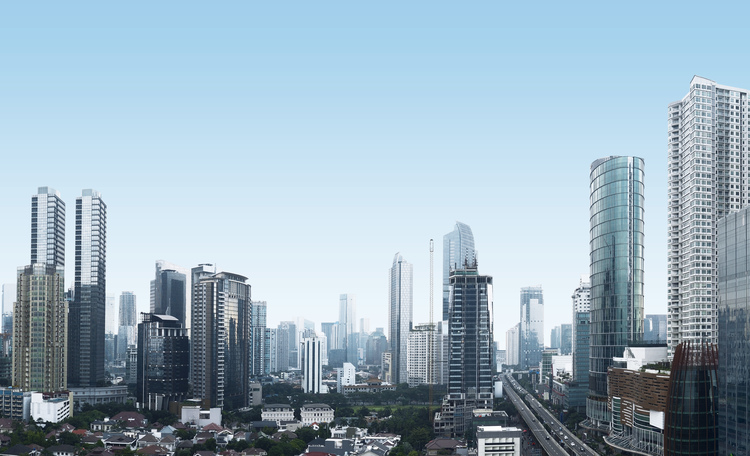
MarketBeat
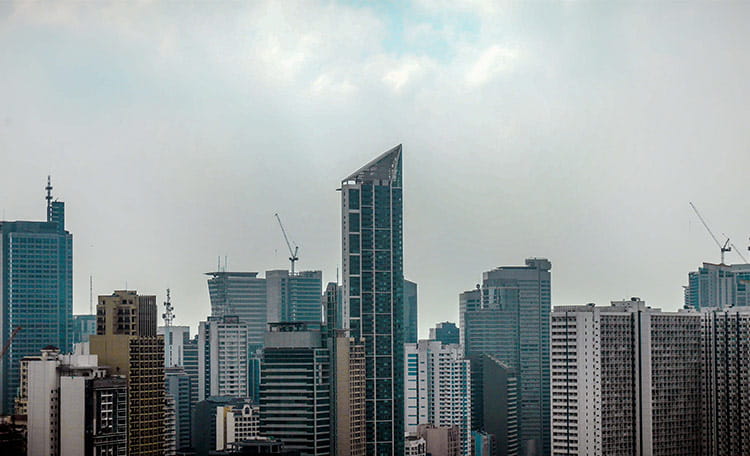