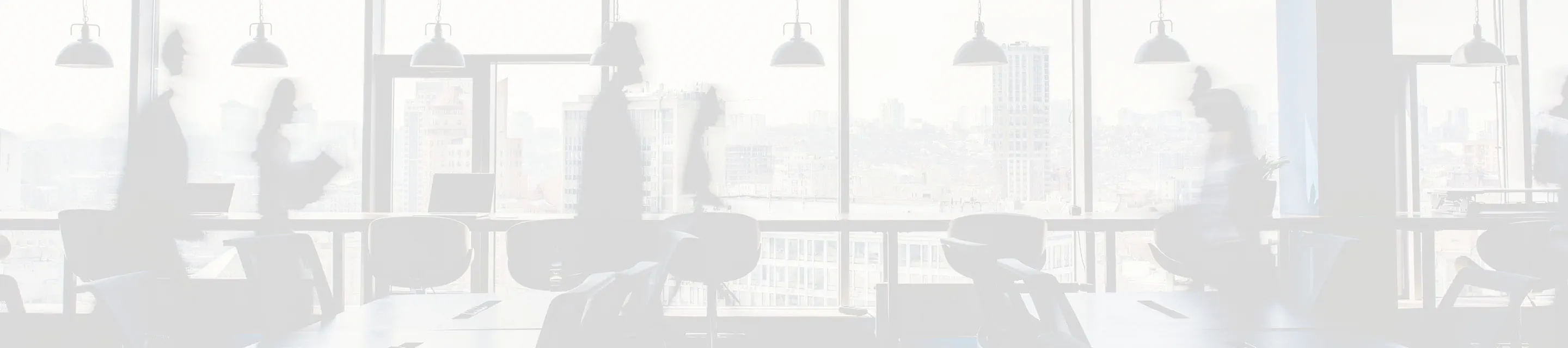
Commercial Real Estate Insights
Most Recent
Research • Economy
Midpoint 2025 | U.S. Economic & CRE Outlook
Article
Northeast Industrial Labor Report
Article • Investment / Capital Markets
6/16/2025
Healthcare
Research • Investment / Capital Markets
Healthcare Capital Markets 2025 Outlook
Research • Investment / Capital Markets
Travis Ives • 8/23/2024
Hospitality
MarketBeat
Research
Unpacking the Strength of New York's Hotel Market
Our Valuation & Advisory team explores three market-specific factors that will limit hotel supply while driving room rates higher.
Research • Food & Beverage
Elaine Sahlins • 7/23/2024
Industrial & Logistics
Article
Northeast Industrial Labor Report
Article • Construction
A Blueprint for Suburban Transformation
Article • Construction
David Hoebbel • 6/2/2025
Research • Construction
Jason Price • 5/22/2025
Office
Article • Economy
Research • Workplace
Experience per Square Foot Instant Insights
Investor
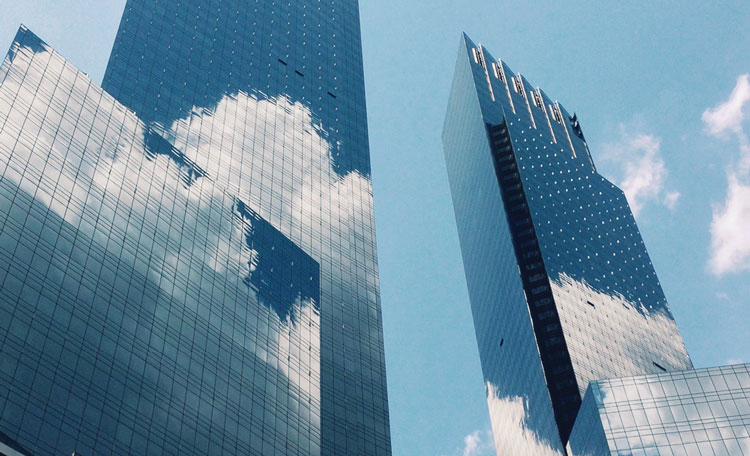
Article • Investment / Capital Markets
Market Matters: Exploring Real Estate Investment Conditions & Trends
Research • Investment / Capital Markets
Abby Corbett • 6/5/2025
Research • Investment / Capital Markets
Dominic Brown • 6/5/2025
Research • Investment / Capital Markets
Sukhdeep Dhillon • 6/5/2025
Research • Investment / Capital Markets
Adrian Ponsen • 6/5/2025
Research • Investment / Capital Markets
Sam Tenenbaum • 5/1/2025
MarketBeats
MarketBeat
Multifamily
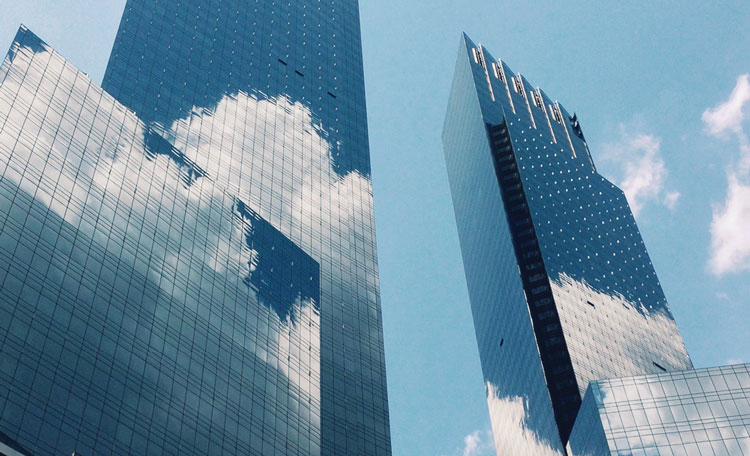
Article • Investment / Capital Markets
Market Matters: Exploring Real Estate Investment Conditions & Trends
Research • Valuation
U.S. Senior Living & Care Investor Survey and Trends Report
Research • Investment / Capital Markets
Sam Tenenbaum • 5/1/2025
Retail
Research
2025 U.S. Retail Fit Out Cost Guide
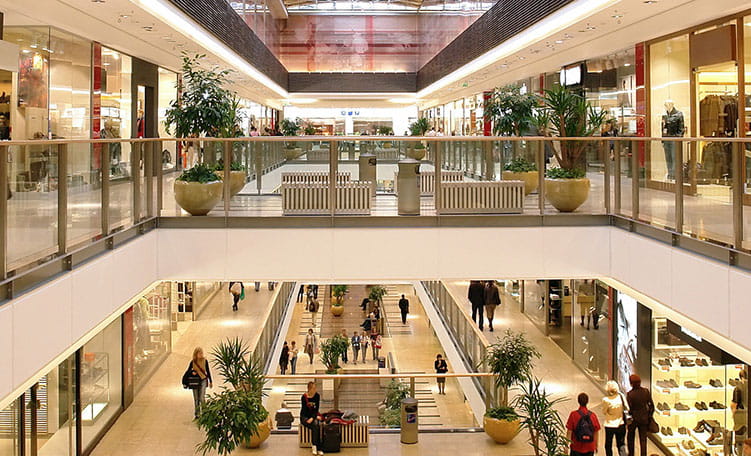
Insights
The Future of B Malls: Transforming Challenges into Opportunities
Article
James Bohnaker • 5/6/2024
Article • Financial Services
John McWilliams • 12/11/2023
Sustainability & Wellness
Research • Sustainability / ESG
Industrial Logistics Climate Risk Outlook
Research • Sustainability / ESG
Climate Risk Global Cities Outlook
Article • Sustainability / ESG
Megan Pendill • 9/17/2024
Technology
Research • Technology
Asia Pacific Data Centre Investment Landscape
Insights • Technology
Asia Pacific Data Centre Construction Cost Guide
Article • Technology
Megan Pendill • 8/1/2024
Research • Technology
Gregory Rogalla • 7/25/2024
Insights in your inbox
FEATURED MARKETBEAT REPORTS
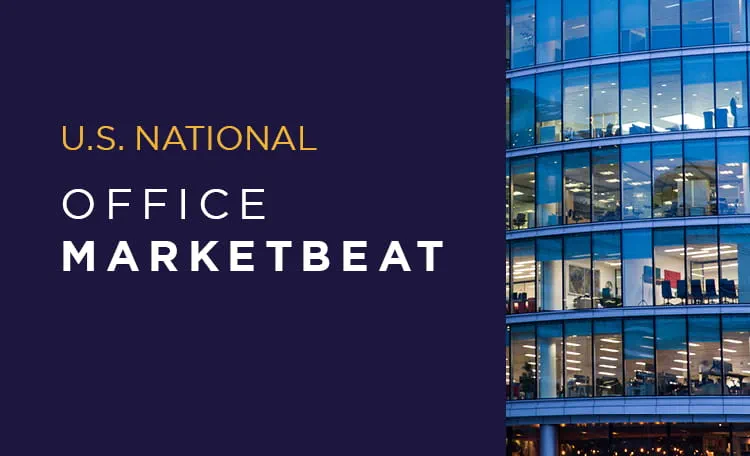
MarketBeat
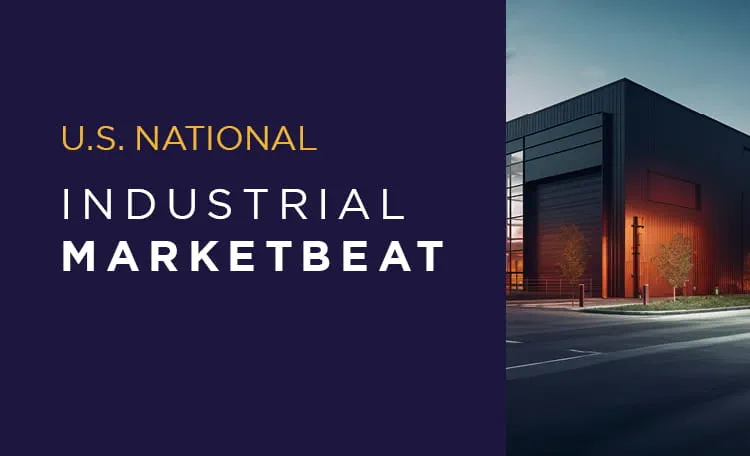
MarketBeat
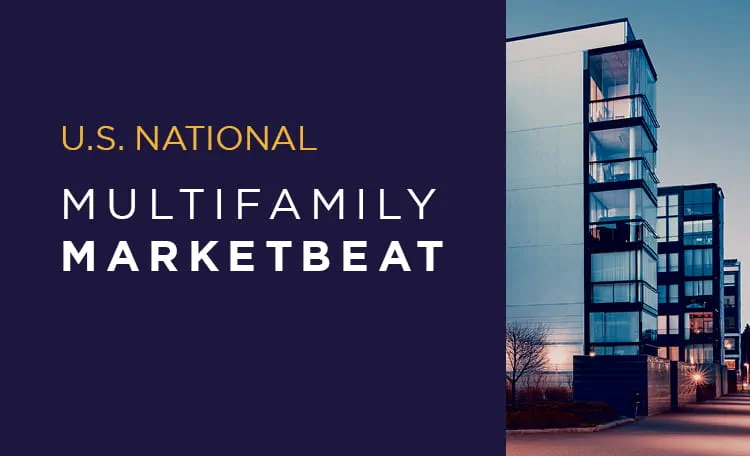
MarketBeat
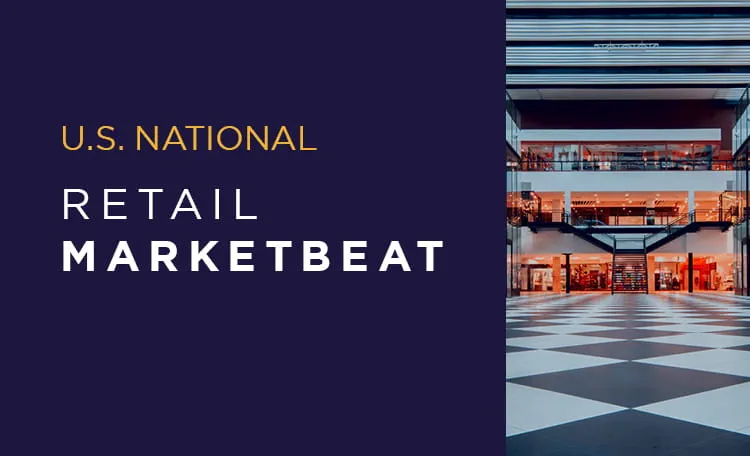