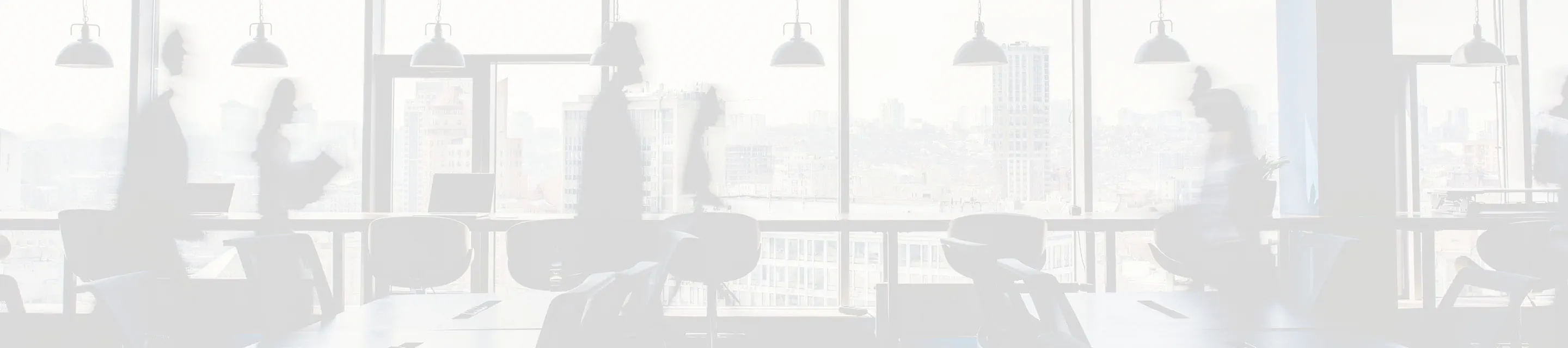
Commercial Real Estate Insights
Most Recent
Research • Investment / Capital Markets
MOB Capital Markets Midyear Update
Research
Healthcare
Research • Investment / Capital Markets
MOB Capital Markets Midyear Update
Research • Investment / Capital Markets
Travis Ives • 8/23/2024
Hospitality
MarketBeat
Research
Unpacking the Strength of New York's Hotel Market
Our Valuation & Advisory team explores three market-specific factors that will limit hotel supply while driving room rates higher.
Research • Food & Beverage
Elaine Sahlins • 7/23/2024
Industrial & Logistics
Research
Research • Construction
Article • Supply Chain
Benjamin Harris • 8/5/2025
Office
Article
Corporate Relocation: A Guide to Moving Your Office
Research • Workplace
Reimagining Urban Real Estate Portfolios
Reimagining cities could unlock $120+ billion in U.S. CRE value. In Reimagining Cities: Disrupting the Urban Doom Loop, Cushman & Wakefield and Places Platform, LLC identified a clear north star: the optimal mix of real estate diversity that drives both higher real estate values (on a price per square foot basis) and stronger economic growth (GDP).
Investor
Research • Investment / Capital Markets
MOB Capital Markets Midyear Update
Research • Investment / Capital Markets
Top Trends Across Cushman & Wakefield’s Multifamily Portfolio
Research • Investment / Capital Markets
Abby Corbett • 7/30/2025
Research • Investment / Capital Markets
Rebecca Rockey • 7/29/2025
Research • Investment / Capital Markets
Abby Corbett • 7/29/2025
Research • Investment / Capital Markets
Dominic Brown • 7/29/2025
Research • Investment / Capital Markets
Catherine Chen • 7/15/2025
MarketBeats
MarketBeat
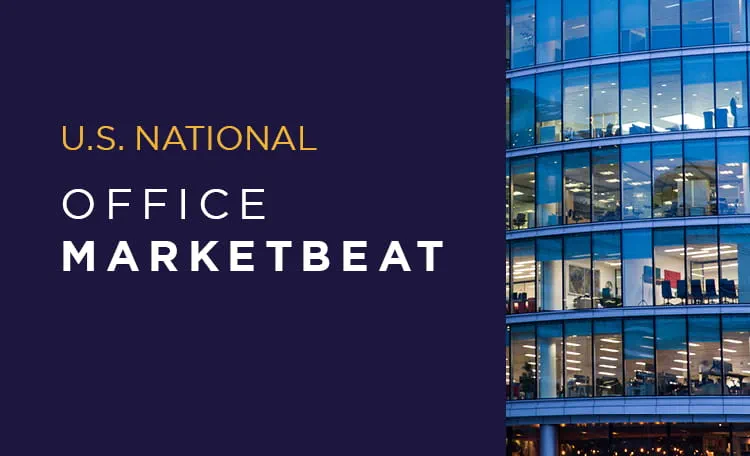
MarketBeat
Multifamily

MarketBeat
Research • Investment / Capital Markets
Sam Tenenbaum • 8/1/2025
Article • Investment / Capital Markets
6/16/2025
Research • Valuation
Zach Bowyer • 6/10/2025
Retail
Research
2025 U.S. Retail Fit Out Cost Guide
Insights
Barrie Scardina • 4/21/2025
Article
James Bohnaker • 5/6/2024
Sustainability & Wellness

Research • Sustainability / ESG
Research • Sustainability / ESG
Industrial Logistics Climate Risk Outlook
Article • Sustainability / ESG
Megan Pendill • 9/17/2024
Technology
Research • Technology
Asia Pacific Data Centre Investment Landscape
Insights • Technology
Asia Pacific Data Centre Construction Cost Guide
Article • Technology
Megan Pendill • 8/1/2024
Research • Technology
Gregory Rogalla • 7/25/2024
Insights in your inbox
FEATURED MARKETBEAT REPORTS
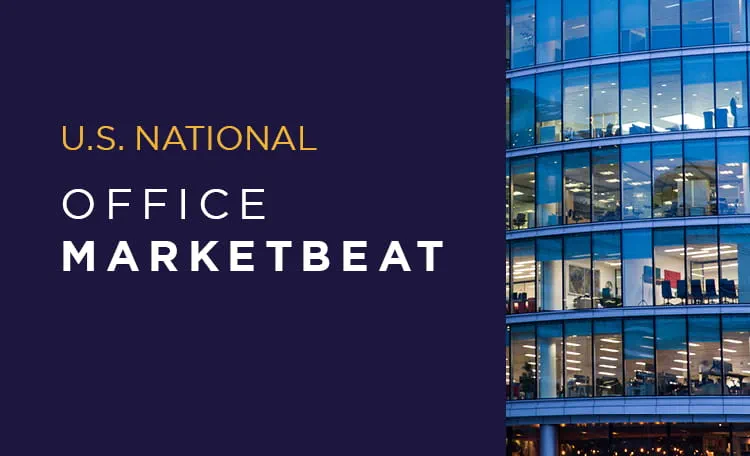
MarketBeat
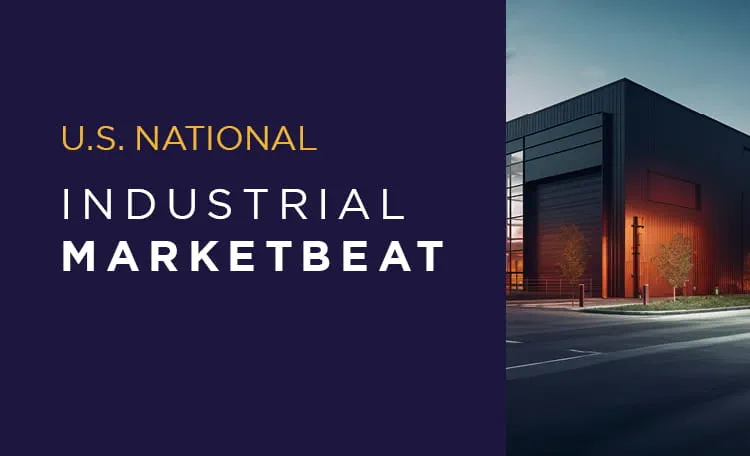
MarketBeat
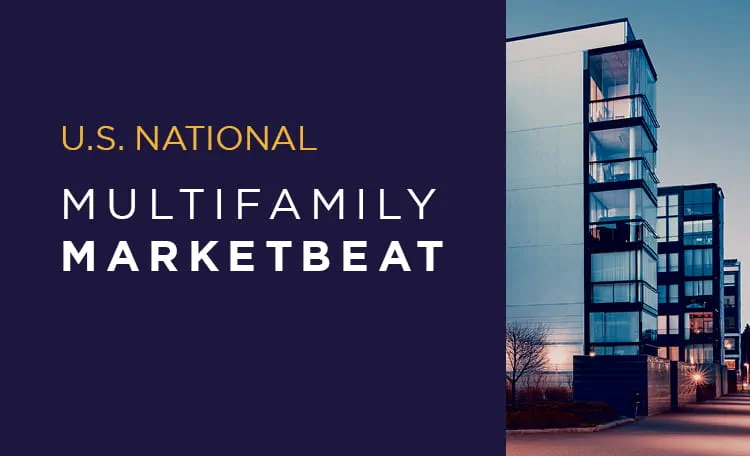
MarketBeat
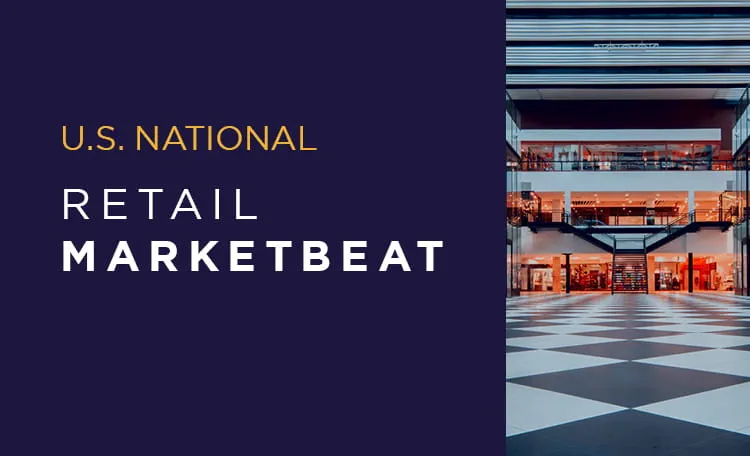